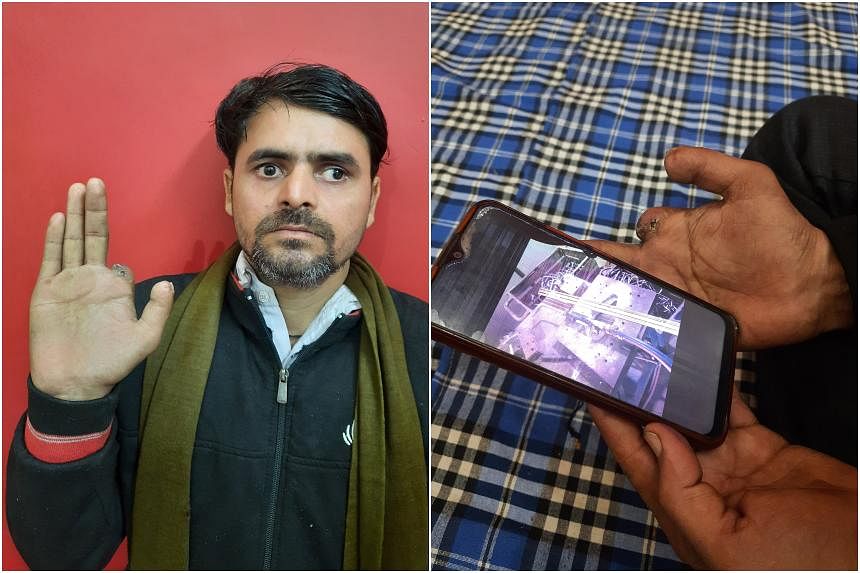
NEW DELHI – In 2022, the Indian vehicle market crossed a significant milestone when it overtook Japan in sales, making it the third-largest auto market for the first time. More than 4.25 million units were sold as manufacturers revved up production following two sluggish pandemic years.
India also exported close to 5.6 million vehicles in FY22, up 36 per cent from FY21. But this revival has come with a bloody cost – a spurt in injuries among workers employed in firms that produce spare parts for the manufacturers.
In just the two key manufacturing hubs of Gurgaon and Faridabad in Haryana state alone, this number jumped from 531 in FY2019-20 to 803 in FY2021-22, according to a December 2002 report by Safe in India Foundation (SII), a non-profit headquartered in Haryana.
But the problem is a national one, said the report, with several thousand workers losing their fingers every year in automobile manufacturing hubs across the country due to unsafe working conditions as well as other factors such as fatigue. This inflicts a “devastating economic and physiological impact” on injured workers and their families, it added, besides adversely affecting the industry’s professionalism and labour productivity.
Industrial accidents in India are frequent and responsible for hundreds of fatalities each year, with many more injuries. In 2020, the government recorded 3,882 countrywide incidents of injury, including 1,050 fatal ones, in the entire manufacturing sector. This is a gross undercount though; the SII estimates that the 68 injuries reported for Haryana, for instance, are not even 5 per cent of the total figure for the state.
The foundation focuses on crush injuries in the manufacturing sector, but its focus on the automobile industry comes from the fact that more than 80 per cent of instances of finger injuries in Haryana and Maharashtra are traced back to this large sector.
India’s automobile industry employs around 37 million workers directly and indirectly. It also contributes 7.1 per cent of the country’s gross domestic product and 49 per cent of its manufacturing GDP.
Mr Shakil Mohammad, 30, a migrant worker from Uttar Pradesh state, had his right palm crushed and severed by a power press machine in Faridabad on Nov 14.
Such machines shear, punch and shape metal sheets into a required form that later makes up spare parts for vehicles. These machines’ in-built safety sensors or guards to prevent injuries are often missing or defective – symptomatic of lax workplace safety compliance in India.
More than half of the 3,968 auto sector worker injuries reported to SII in the past six years occurred on these dangerous power press machines that are poorly maintained, resulting in malfunctions. A majority of the machines responsible for these injuries also lacked the safety sensors they should have had.
In Mr Mohammad’s case, the die – a metal block used to stamp out shapes in metal sheets – plunged down suddenly as he was fitting a new metal sheet into the machine.
He said he did not press the machine’s pedal that causes this action, adding that the machine’s safety sensor that would have prevented his injury in case of such an advertent push on the pedal was also broken, with “pieces lying on the ground”.
With his last complaint about a broken safety sensor on another machine overlooked, he continued working on these machines as his supervisors hounded him to keep up productivity. “Had I told them I will not work, they would have asked me to leave,” he told The Straits Times. As he needed his monthly salary of about 13,000 rupees (S$211), he had little choice but to carry on.
R R Autotech, the factory where Mr Mohammad worked, has around 240 employees and produces spare parts for top vehicle firms, including Indian market leader Maruti Suzuki.
A company spokesman said Mr Mohammad was injured due to his own “mistake”, as he was oiling and cleaning the machine without switching it off. “His foot fell on the pedal because of which the die came down,” the spokesman said, adding that the machine had working safety sensors, but the worker had turned one of the two aside while cleaning. Mr Mohammad refuted this explanation.
Fatigue is another key factor that contributes to injuries. As many as 12 per cent of the injured workers documented for 2021-22 in the report said they were working past their 12-hour shift at the time of the accidents.
Many power press injuries, which lead to the loss of an average of 2.3 fingers per incident, also occur to workers who, legally, should not even be operating these machines. Employed for other roles, they are deputed to operate these dangerous machines with little or no training due to manpower shortage.
Injured workers are compensated through the government Employees’ State Insurance Corporation (ESIC) scheme. Benefits include free treatment, a temporary disability allowance as well as a lifetime inflation-indexed pension pegged to the level of disability.
But more than 60 per cent of injured auto sector workers receive their ESIC card only after their accident, even though employers collect contribution amounts from workers regularly, the SII report noted. This delays benefits, even leading to rejection in certain cases.
In Mr Mohammad’s case, he is receiving free treatment under this scheme and the paperwork for other benefits is being processed. He has also received ex-gratia assistance of around 6,500 rupees from his contractor, but this is not enough to meet his living and room rent expenses, now that he is out of work.
Since its first annual report in 2019, SII said industry stakeholders such as the Society of Indian Automobile Manufacturers and the Automotive Component Manufacturers Association have engaged with it to try and prevent supply chain worker accidents.
Progress, however, remains stymied for the lack of an industry-level momentum to tackle this issue, such as what was seen in Bangladesh following the Rana Plaza disaster that galvanised top brands, the local government and other stakeholders to come together and improve safety and professionalism in the country’s garments sector.
“We need the industry and the government to sign a pact to improve safety, productivity and professionalism in the automobile sector supply chain, with a phased implementation plan,” said Mr Sandeep Sachdeva, SII’s co-founder, adding that the auto industry has the scale, knowledge and influence over both the government and its suppliers to drive such an initiative.
Specific recommendations for the government include a stronger workplace regulation, contrary to proposed dilutions in the Occupational Safety, Health and Working Conditions Code and reversing a trend of falling factory inspections. The government has also been urged to set up a confidential helpline for workers to report unsafe conditions and factory accidents, helping end chronic under-reporting of injuries in the auto sector.
While this problem around unsafe working conditions is not limited to India, Mr Sachdeva told ST these accidents represent an “opportunity for India to accelerate its natural progression towards better working conditions”. This will be in sync with one of the targets under the United Nations’ Sustainable Development Goals that seeks to protect labour rights and promote safe and secure working environments for all workers.
It is a goal that consumers, too, have a role in. “Every vehicle purchaser and a buyer of components has to question brands about workers safety and working conditions in the deeper supply chain,” added Mr Sachdeva.